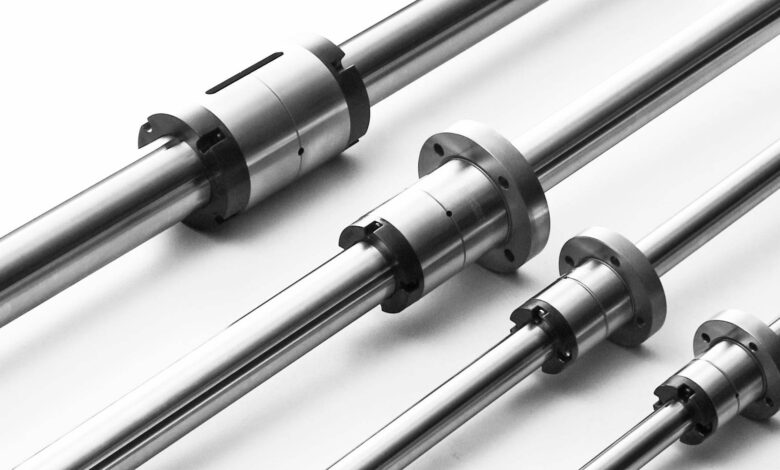
5 Ways to Increase Ball Spline Load Capacity – 2024 Guide
There are a lot of machines out there that require both rotational and linear motions. Some of those are in Robotics, some in medicine, but also in oil, gas, and water exploration. Further examples would be automation and packaging equipment, or even honing devices. So when this mixture of motions is happening, there are few solutions available out there. With them, we can make sure the machines are functioning at maximum capacity.
Previously we employed a straight sliding spline, but a far more beneficial answer is a ball spline. With them, there is lighter interference and a more limited inclination to bind. With ball splines, we have almost no friction with linear motions when we are transferring energy. You can simply imagine the next comparison the ball spline is for splines what ball screws are for regular screws. So if you just want to find some of them or learn more about them, check out tuli-shop.com, a great place to find everything one might need. But if you are interested in ways how to increase the ball spline weight limit, we have some of the answers for you here.
1. Number of groves
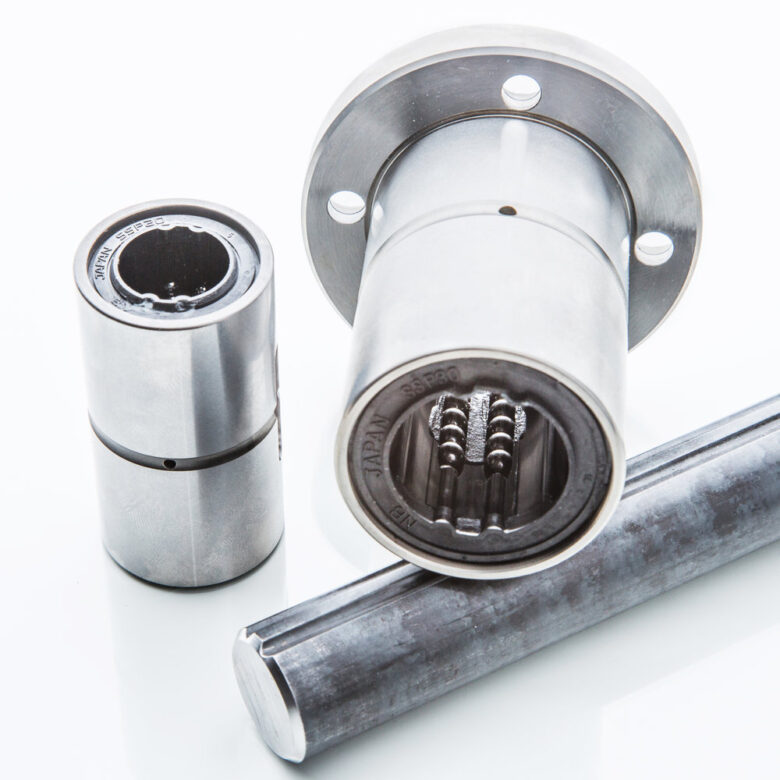
So we already established that spline balls are better than slide shafts. Load capacity and life span are in a much better position than sliders of comparable dimensions, with bigger touch fields. If you wonder how much they are better, the answer is from half a dozen to a dozen times. Now, the volume of groves can vary and go from 2 to 6, depending on the type. But there could still be some problems on the horizon. When the number is higher, it takes too much room on the shaft, which is not ideal. All this means that the nut’s active ball paths are in problems since there is no opportunity for balls to circulate continuously. That is why when dealing with this one, some additional responsibility is a must, as the last thing we want is for them to drop out of the nut since that is what will exactly happen when the shaft and the nut are set apart. It is all a reason more why it is always the best possible option to pick the one with the four grove combination. That is because it is simply the ideal version for most machines.
2. Groves shape
So when it comes to groves patterns, the decision usually needs to be made within balls that make a connection with the raceway grooves at two positions or four positions. Elliptical grooves help out the balls to make a connection at contrary positions. At the same time, there is plenty of room on the ground balls that are straight from those which are connected. Even here, there are possible problems, like when there is a shift to the circling of the shaft since that can cause a reaction from nuts. Since four groove systems have greater contact zones, that means that those parts of the balls on the inside must move in circles quicker than the other pair. That can often lead to slippage and ends in even more friction. Using circular grooves is therefore advised, especially when dealing with tinier more prone to friction ball splines. There are other systems of shaft types as well. Half triangular protuberances together with spline shaft are excellent for larger loads. However, it may be a bit more complicated to use this type of device. The main reason is that they are vulnerable to fluctuations. That is because they have a problem with staying straight all the time. In general, the more flexing and distorting twisting is allowed, the more useful.
3. Nuts size
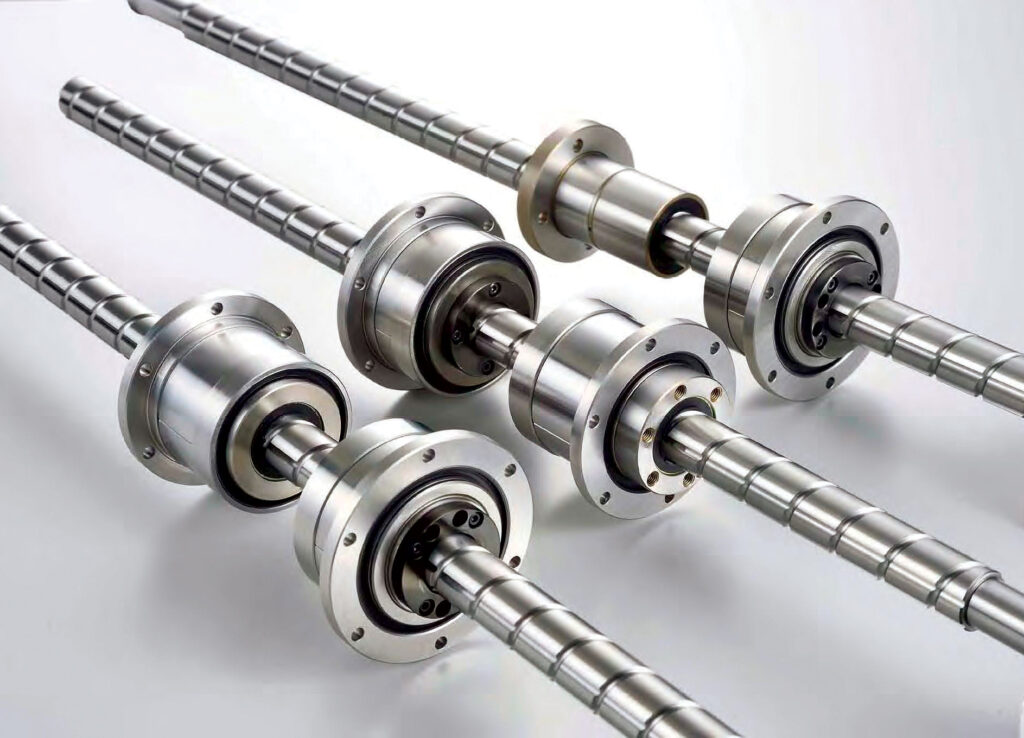
The thing to realize is that, usually, 50 % of the balls are working, and the other 50 % are in the recirculating trail. What we are looking for is the more efficient use of nuts size. And it is quite simple, and the more of them work – the larger is the load capacity, which means that a great system will always use as much of them as it can.
4. Nuts toleration
The ideal system will alter the form of the balls in the nut and the shaft itself. The goal here is to make sure there is no repercussion. And for that, we need to have perfect angles of connection. What we are ideally looking for is to have the outside of the barrel aligned with different sizes. That will help us immensely in managing the space from one ball to another. It is crucial to have everything preloaded separately. That way, everything about how many oscillations and inconstancies we have will get reduced to a minimum. Industrial preload will make it much more efficient since the machine will be able to work even in harsh conditions.
5. The rigidity of the shaft
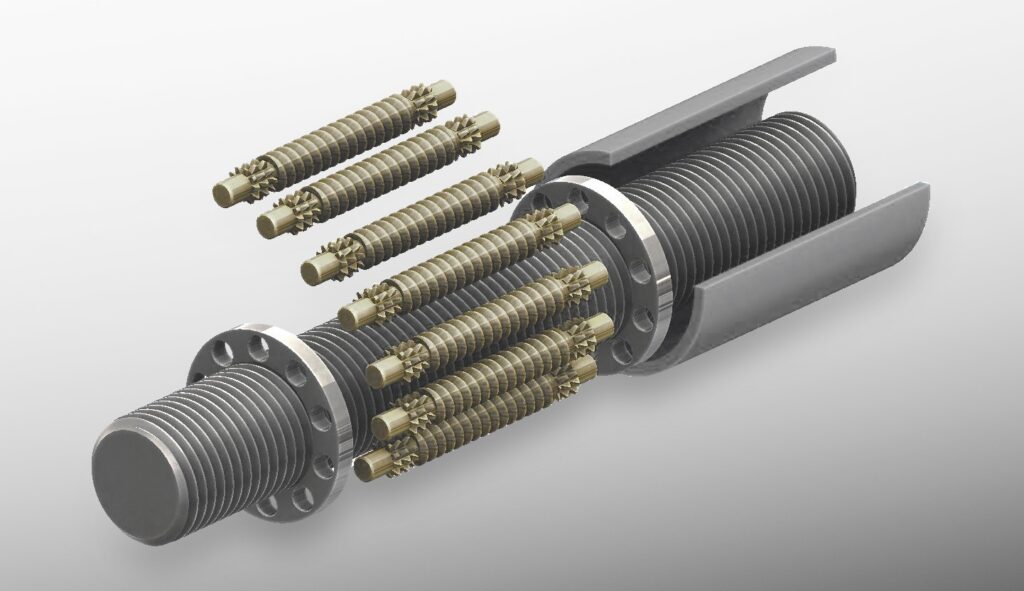
Another way to increase load capacities is to have a larger spline shaft. That way, it can have quicker rotations and reduce fluctuations as well. There are many different types of it, and some are drawn steel bars, but we also have ground and precision-ground ones. There are other ways to categorize them by industrial standards. But to summarize, it all comes to their effectiveness, and whether it is high, medium, or low. And the best solution for each one of us depends on the individual needs and the type of work that needs to be done.
Conclusion
So there you have it. The topic is complex, and there are many ways to achieve this and make the most of the load capacity. When it comes to what can we do and what should we select, it can be highly distinctive to our situations and needs. Load capacity is the crucial factor when determining which ball spline to go with, but life expectancy, speed, and room between them are also essential and something to keep in mind when making a choice. Hopefully, we have succeeded in helping you in making the correct choice.